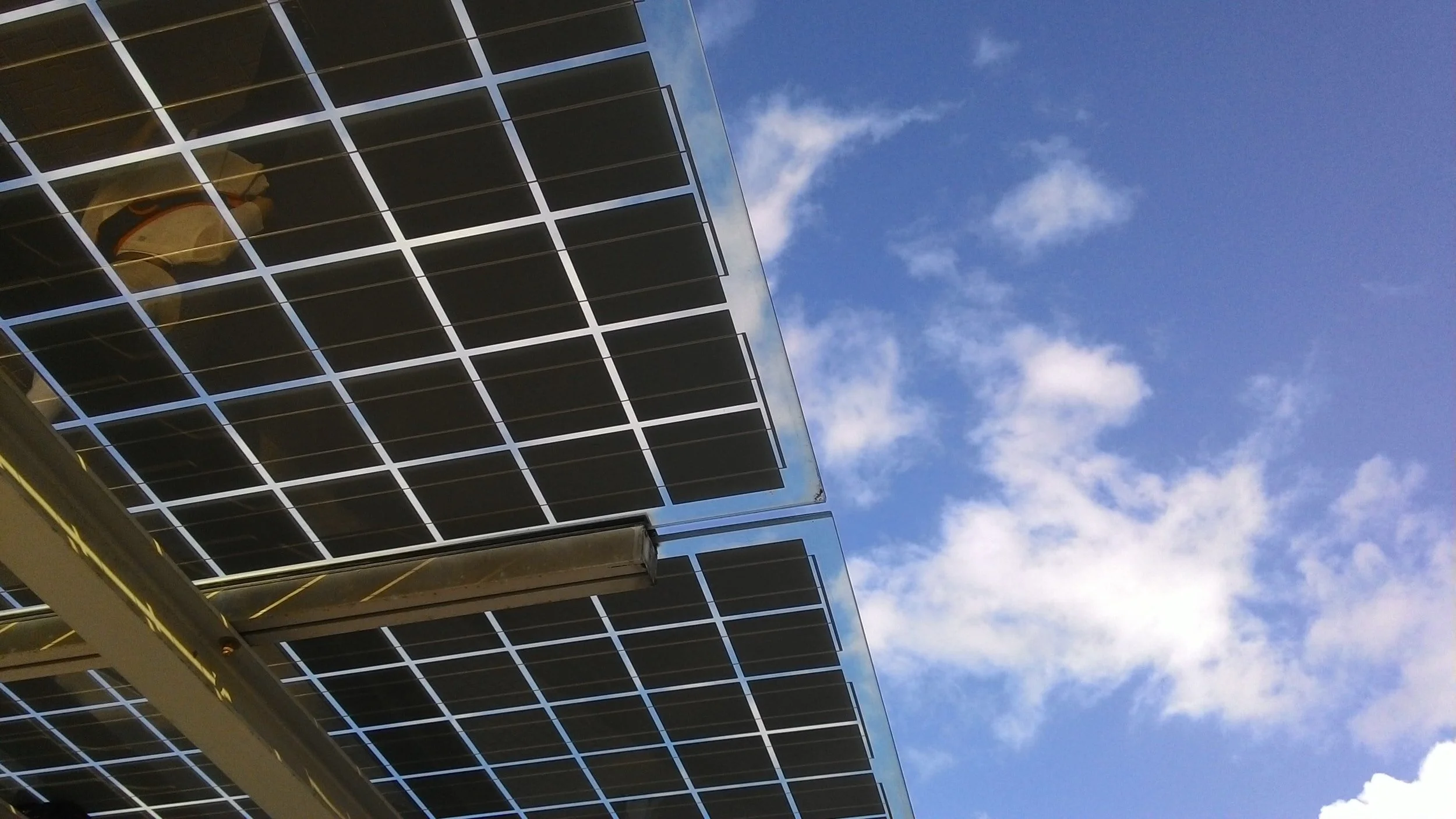
Welcome to our Blog.
Learnings, teachings, news and know-how of the solar industry.
Issues of Balance of System
BoS of a solar PV plant constitutes all the components of a PV system other than the modules. These components makeup roughly 15-20% of solar purchasing and installation costs and account for the majority of maintenance requirements. It is through the balance-of-system components that we control cost, increase efficiency, and modernize solar PV systems. It has been observed in the industry that BoS care is sometimes ignored in comparison to the modules. We are sharing some of the similar cases in which owners and developers learned this in the hard way that BoS holds as important a place in the system as the solar modules.
Design level issues
At a 12.5 MWp plant in Telangana, we diagnosed serious issues with the tracking system and other BoS components. Some of these issues and suggested recommendations are described below:
• Driveline slip due to slotted joints: The driveline is supposed to act as a rigid member to rotate all the torque struts identically. Since a single driveline is not possible in a plant, it is usually broken into segments and then connected. It was observed that there were long slots in these drivelines which resulted in slipping of slotted joints and improper operation of the whole tracker block. We recommended welding these slotted bolts and creating a permanent connection.
• Lack of sufficient Lightning Arrestors: According to the LA drawings, there were 4 lightning arrestors installed in the plant which were not able to cover all the plant area for protection (the circled area shows the approach of LAs). It was evident from this LA drawing that in any severe lightning episode, the installed lightning arrestors will not be capable of safeguarding every module. After analyzing these drawings, we recommended the installation of 4 additional LAs in the region.
• Health Safety Environment (HSE): HSE protocols are made to ensure the safety of workers as well as visitors in the plant but these protocols were not followed in this plant. For instance, the protocol specifies to install safety signs on all the high voltage areas, under construction areas and other watchful locations to alert the workers/visitors in advance of the risks around them.
Similarly, fire protocols state the strict availability of fire extinguishers near transformers, switchyard, inverter station, control room, and other fire-prone areas which were nowhere to be found.
We recommended following the HSE protocols and brief everyone the precautions needed to be taken until HSE protocols are installed in the plant.
• Drainage issues: The soil in the location was clayey. Since clayey soil consists of very fine particles and not many organic materials, it’s usually sticky and compact. As a result, this soil is incapable of draining well and increases the water-logging issues wherever present. We suggested a drainage system that included culverts, internal drains of 9.8 km, and peripheral drains of 5.5 km drainage and Hume pipes to connect the drainage path to overcome this.
Water Logging Due to the nature of the soil
• Module cleaning system: The plant had unavailability of a proper water storage system and therefore water tankers were brought from outside for cleaning modules. The water brought in tankers was hard (TDS value was >500 PPM) which escalated the scaling on the modules and might reduce the generation output in the long run. Also, the majority of water in the tank was wasted as it was handled by unskilled workers. We suggested installing a module cleaning system (MCS) in the plant along with RO and borewell systems to eliminate this problem permanently.
• Plant approach road: The approach roads in the plant were in a dreadful condition and the situation was even worse during the rainy season. This created issues in providing basic care to the plant. The O&M teams faced trouble in reaching the site and took them a considerable amount of time to clear the faults than necessary. We suggested a proper road construction strategy along with the layout of the most efficient road for the plant.
Approach road in the plant
2. At another 104 MWp plant in Maharashtra, we observed the below-listed issues in the plant.
• Electric poles in between the modules rows: This location had some electric poles in between the rows of the modules which cast a shadow on the modules and resulted in a lower generation. We suggested removing these electric poles to reduce the shading losses.
Pole in between the module array
• Issues in the structure: We observed white rust on several braces which might lead to early deterioration of the structure members.
White rust on structure member
One brace member was found missing for most of the structures running along the East-West direction. This brace was ensuring stability in EW direction and therefore it was essential to add these braces as per the drawings.
Drawing showing missing brace in one of the tables.
Operation-level issues
AC cables attached in place of DC cables: In a 2 MW plant in Maharashtra, some DC cables were clipped from the side of the modules and robbed by the locals. The local team attached the AC cables of 2.5 mm2 in place of the DC cables of 4 mm2 as an immediate solution. Since the size of the AC cables were lesser than the DC cables, it reduced the current carrying capacity of the cables. At the same time, the voltage drop was increased (because length remained the same and diameter was reduced) which changed the maximum operating point of the system and the complete system started underperforming. Another issue with this remedy was that as per standards, double insulation cables are used on the DC side but they replaced the cables with single insulation cables which increased the risk of insulation failure, fire, or shocks as AC cables have less insulation.
Another major issue was using insulation tape to make the connections instead of proper MC4 connectors.
AC cable in place of DC cable
Cables lying on the ground
2. Higher temperature differences on the cable end-termination:
At a 5.75 MW plant in Maharashtra, high temperatures were observed at the terminations during the thermography of the BoS (IGBT section of the inverters and SCBs). It was observed that the cables were of copper, and lugs used for end-termination were of aluminum which caused this high-temperature difference. We suggested changing these aluminum lugs with bimetallic lugs to reduce the temperature difference.
Also, in most of the SCBs, the WAGO terminal block of strings was found with a high-temperature difference (approx. 20-30℃), for which we suggested replacing them as the terminal block deteriorated. In a few cases, SCB to Inverter outgoing DC cable and heat sink were also found with hotspots, for which we suggested tightening loose connections and replacements of rusted end-termination lugs.
DC section of the inverter: The temperature difference between 2 DC cables at termination end is 29.5℃ and 40.1℃ in 1st and 2nd image respectively
Aux. transformer: LV side - Temp diff = 27.1℃
Inverter- transformer: LV side - Temp diff = 40.9℃
Temp diff. = 50.8℃
Temp diff. = 13.6℃
In the plant-side switchyard, we observed one phase (out of three phases) of the isolator had a maximum temperature of ~180℃. After proper visual inspection, it was found that the panther conductor end-termination was not done properly due to which there was a loose connection. Therefore, we suggested immediate rectification of the end-termination.
Maximum Temp. = 180.2℃
3. Burnt SCB due to improper isolation - In a site in Rajasthan, a technical team was running IR measurements on SCB’s strings, completely unaware that one of the strings had ground fault because of which one of the SCB got burned. There were 2 main principle reasons behind it.
(i) Before the measurements, the technical team did not open the DC isolators which is a basic rule before taking any measurement.
(ii) While opening the fuse, they opened it very slowly which caused a spark and burnt the strings along with the SCB.
Burnt SCB because of ground fault
There was one more problem on the site which worsened the situation further. When the technical team reached for the fire extinguisher nearby, it was empty and therefore it took considerable time to get a hold on the fire. Until then, much of the cables were burnt which could have been saved if the fire extinguisher was filled. We suggested the field team to check all the fire extinguishers and ensure that they are filled to tackle any future episode like this.
4. SCB’s SPD issue due to earthing terminal not earthed: Surge Protection Device (SPD) is designed to limit transient overvoltages and divert current waves to the earth, to limit the amplitude of this overvoltage to a value that is not hazardous for the electrical installation and electrical switchgear and controlgear. This SPD is located inside the SCB and has 3 terminals: positive, negative, and earth. We have observed that positive, negative, and earth terminals of SPD are connected with the SCB but many times, technical teams ignore connecting the earth terminal of SPD to the ground. As a result, when these surges occur, SPD doesn’t have a path to divert the current waves to the earth and can’t protect the electrical installations from overvoltages. We observed one such fault in a 15 MW plant in the state of Gujarat and recommended to earth all the SPDs in the plant.
Earthing not provided to SPD
To conclude, the BoS system is responsible for the optimum working of the plant. A little ignorance can prove hazardous in the long run and therefore it is pivotal to look for little details while designing and operations of the BoS to ensure the best performance.
The big picture is - Attention to small details always shows the best result.