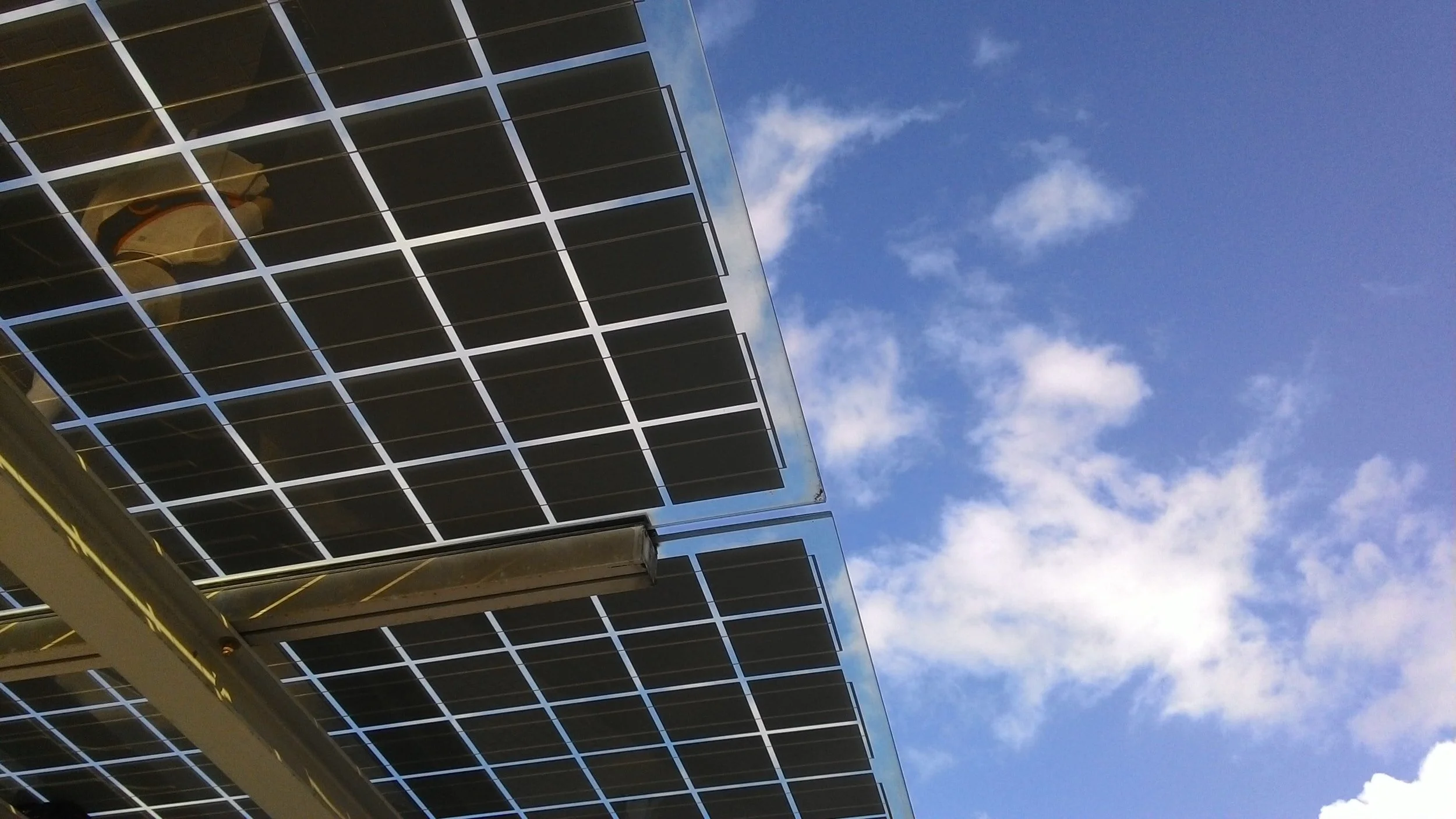
Welcome to our Blog.
Learnings, teachings, news and know-how of the solar industry.
Warranty Claim A Success Story of on-site testing
Executive Summary
PVD conducted a diagnostics study of two solar plants of 5.75 MW each for a client in Rajasthan and Maharashtra and was successful in getting a warranty claim worth INR 1 Crore for the client. We would like to share the process that we followed for the benefit of our readers.
The plants were 8 years old and had 41,060 modules of 280 Wp poly-crystalline technology. As a first step, we conducted a basic diagnostics study (On-field I-V curve measurement for sample strings and modules, thermal imaging of modules & BOS, and EL imaging of modules). This was followed by a detailed diagnostics study (I-V curve measurement of all the modules and EL imaging on a sample basis for modules) for both the plants to understand the level of degradation and any other issues in the plant that might be impacting the generation. During the site inspection, we observed that 80% of modules had degradation of over 7.5% (threshold expected degradation) while ~60% of modules had degradation of over 10% (threshold value of stepwise performance warranty clause). EL Imaging and Thermal Analysis identified the reason for degradation rates as severe solder failures causing hotspots and corrosion. As these defects are directly related to manufacturing and material quality, our client requested a warranty claim based on these reports. Post multiple rounds of discussion with the module manufacturer, and testing of 10 modules at a 3rd party lab by the module manufacturer, the claim amount was approved.
Some of the challenges that we observed in the warranty claim process include:
Establishing whether or not there is degradation in the modules for reasons attributable to the OEM
Estimating the total “power loss” due to accelerated degradation
Mutual acceptance of the replacement criteria by the client and OEM.
Aligning on a measurement methodology with the OEM
Establishing the onus of power loss on OEM
Here’s how PV Diagnostics addressed these issues:
Establishing degradation and cause of underperformance through diagnostics
Our Diagnostics study is highly exhaustive, taking every aspect into consideration. The steps followed in this diagnostics study was as follows
The first step in a diagnostics study is to select a sample of modules and strings for IV curve measurement, in such a way that the sample is representative of the plant. We use statistical sampling to estimate a sample size of 95% confidence level and a 5% margin of error.
Followed by IV measurement, we conduct thermography for the modules. In this case, we conducted thermography for all the modules
For the next step, we selected a sample for EL Imaging, while ensuring no sample bias.
A complete visual inspection followed by BoS components inspection was done next.
There are multiple correction factors used to eliminate experimental uncertainties while measuring power degradation, details of which can be shared individually if you are interested to know more.
Please see below, the key results from the diagnostics study at one of the plants:
Plant size: 5.45 MW
Average degradation in modules: 12.5% (Expected degradation as per module warranty = 10%)
Percentage of modules degraded more than 10%: 81.2%
Percentage of modules with severe hotspots: 3.13%
Percentage of modules with moisture ingression/Corrosion: 78.8% (from the selected sample)
Percentage of modules with solder contact defect: 22%
Hotspot due to solder contact failure
Solder contact failure
Hot spot due to solder contact corrosion at busbar and the corresponding failure
Corrosion
Estimating power loss due to accelerated degradation
After establishing degradation rates and causes of underperformance, we estimate the access power loss. This calculation is based on the average specific generation, plant capacity, and access degradation. The combined access power loss on these plants was 80.17 kWh/kWp/year.
Concluding results and supporting the claim process
Once high manufacturing defects were confirmed in the modules, our client contacted the module manufacturer sharing on-site detailed reports and their concerns. The manufacturers processed their request in a below-listed manner.
They analyzed our reports and requested a sample from both plants for report validation.
As per ISO 2859 sampling criteria, the client sent 5 modules each from both the plants after mutual consent.
The transportation and testing expenses were covered by the module manufacturer.
EL Imaging, Flash testing, and visual inspection was conducted for all the 10 modules, verifying that our on-site reports were closely aligned with lab test reports
Defining module replacement criteria
The module datasheet defined rated Vm as 35.2 V and specified that the modules will perform at 90% between 5 to 10 years. That means until 10 years, Vm should be above 31.68 V. After considering this and other field measurement tolerances,
Replacement criteria = Vm < 31.5 V
Module replacement: FINALLY!
According to our field reports, 1591 modules fulfilled this criterion and all those modules got replaced costing around ~INR 1 Crore.
To conclude, getting a warranty claim is a hard but not an impossible task. We are often led to believe that warranty claims are often not successful for smaller developers, but with methodical testing, reporting, and analysis, it would be possible for anyone to get a claim if their case is genuine.
We hope you liked this piece and picked up some insights too.
Please feel free to contact us at ayush@pv-diagnostics.com for more details.
Happy Claiming!!